More than meets the eye in formulation game
About
-
Date
30 June, 2018
-
Location
National
About
Date
30 June, 2018
Location
National
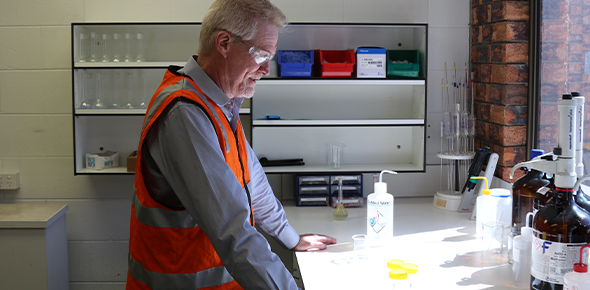
Just the fact Bayer has formulation plants in Australia is a point of interest – they are one of the only R&D companies in the country to have such facilities, and there’s a good reason why they’ve invested in this area explains Mr Clark.
“We want to be close to the market, we want to be flexible, and our two formulation plants enable us to make product as close as possible to market supply requirements as we can,” he says.
“Our job is to take the active ingredient, blend it with other components to turn it into a useable and effective formulation, pack it and then put the product in our distribution centres. Based on the forecast from customers and the orders that come in, it will then get distributed through transport companies to customers.
“There’s obviously a lot of demand volatility based on weather conditions in Australia which can change supply requirements, so to help us level things out regionally, we are part of a network of nine formulation sites Bayer Crop Science has to service the Asia-Pacific Region.”
While many may not stop to consider what goes into getting a product on-farm, it is an involved process, which starts with the formulations themselves being developed globally.
“The products go through a rigorous testing program and registration process, which if we’re only looking from the active ingredient discovery to the formulation stage, could take somewhere around three years, while developing the active ingredient itself can take something like 8 to 10 years,” Mr Clark says.
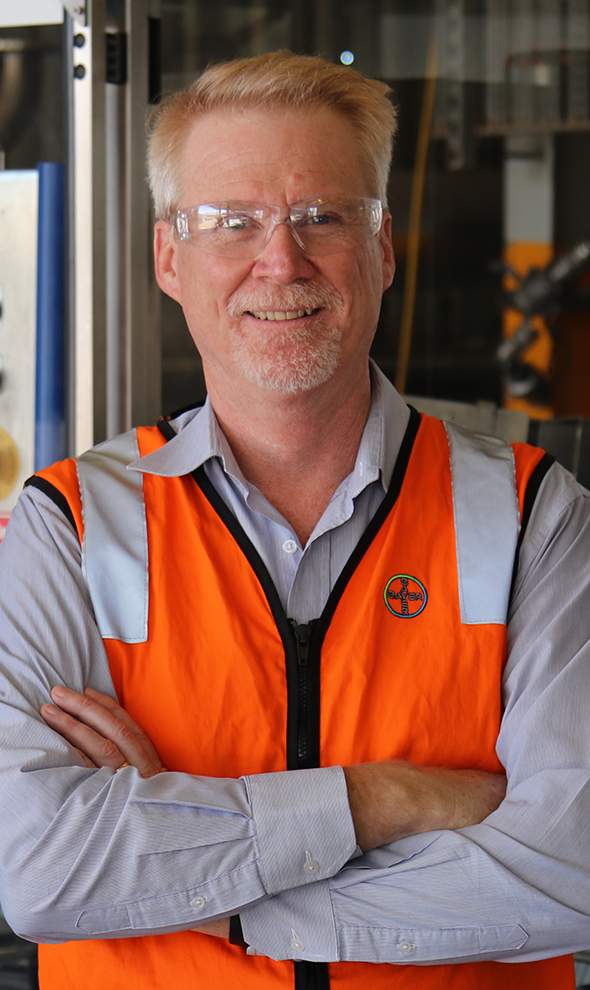
David Clark, Head of Product Supply at Bayer.
“It’s a very long process to get to the point where our Australian formulation facilities are taking the active ingredient and formulating to the registered recipe, and then going through quality testing processes to make sure the product meets specification, before releasing the packaged product to customers.”
It’s critical, according to David Clark, that they follow the specific recipe at the formulation plant to ensure the quality of the end product and compliance with the conditions of the product registration.
“We need to make sure the product performs to the highest possible standard over the largest number of different scenarios faced by end users,” he says.
“If the formulation isn’t optimised it can have an impact on the efficacy of the product, so that’s why it’s important to develop a really robust formulation and then test it very widely before releasing it for farmer use.”
The scope of the work just at the Brisbane formulation plant is impressive, manufacturing around 140 different formulations, and packing them off as nearly 350 different end-use products to supply Bayer’s crop and environmental science businesses in Australia.
“We’ve got six different work centres in Brisbane, each of which focuses on a different product type, so we do suspension concentrates, emulsifiable concentrates, soluble liquids, and we pack granules,” Mr Clark says.
“It’s really important that we manage any cross-contamination - for example, we have separate work centres for herbicides and non-herbicides, so there’s minimal chance of any crossover.”
Every product has a specification it must meet before leaving the site, a process which is underpinned by both a quality control facility and a quality assurance facility working to ISO 9001 and ISO 14000 standards.
“Our laboratory will take samples of every product, and we retain samples to test the product against the specification before it’s released for distribution,” Mr Clark explains.
“We can track all products by batch number, by manufacturing date, and if we ever have an issue, we can trace back to find out what, if anything, went wrong from a formulation perspective.”
It’s clear that, having been in the formulation business for 31 years, David Clark has seen plenty of changes in the formulation industry, particularly around the technology delivering active ingredients to the market.
“There’s been a pretty significant changeover in this industry, back from the very manual days and very big volumes of one active ingredient low-activity products, to today where the volumes are much smaller, and we might have one product with four different active ingredients in it to provide a complete solution,” he says.
“The ways in which we’re formulating probably haven’t changed so much, but the technology that’s packed within the formulation is the thing that’s changed considerably.